Introduction
Overview of Digital Transformation in Manufacturing
Digital transformation in manufacturing refers to the integration of digital technologies into all aspects of the manufacturing process, fundamentally changing how operations are conducted. This shift encompasses everything from the use of connected devices and automation to data analytics and cloud-based systems, all of which enable manufacturers to operate more efficiently, reduce costs, and improve product quality. With advancements in Industry 4.0, manufacturers are leveraging technologies like IoT, AI, and robotics to enhance operational flexibility and innovation.
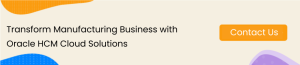
Importance of Innovation in Manufacturing
Innovation has always been the key driver of growth in manufacturing. Today, however, the pace of innovation is accelerating, powered by emerging technologies that allow manufacturers to rethink business models, streamline processes, and meet evolving market demands. The ability to innovate rapidly is crucial for staying competitive in an increasingly digital world. Manufacturers who embrace innovation can create more sustainable and customized products, improve customer experiences, and enhance their ability to respond quickly to market changes. Digital transformation is, therefore, not just about adopting new tools but fostering a culture of continuous improvement and adaptability.
Key Drivers of Digital Transformation
Industry 4.0 and Smart Manufacturing
The fourth industrial revolution, or Industry 4.0, is driving the digital transformation of manufacturing. Industry 4.0 refers to the use of smart technologies like the Internet of Things (IoT), artificial intelligence (AI), machine learning (ML), and advanced robotics to create intelligent and interconnected manufacturing environments. These technologies enable real-time data exchange and analysis, optimizing production schedules, improving product quality, and enhancing supply chain visibility. Smart manufacturing enables manufacturers to produce goods more efficiently and at a lower cost while ensuring greater flexibility and customization in product offerings.
Competitive Pressures and Consumer Expectations
Manufacturers today face heightened competition from both traditional rivals and new entrants that leverage digital technologies. As consumer expectations evolve, manufacturers must adapt quickly to remain competitive. Consumers now demand higher-quality products, faster delivery, and personalized experiences, which means manufacturers must harness digital technologies to meet these expectations. Additionally, global competition forces manufacturers to embrace digital transformation to improve efficiency, cut operational costs, and maintain a competitive edge in an increasingly crowded marketplace.
Environmental and Regulatory Factors
Environmental sustainability and regulatory compliance are increasingly influencing manufacturing strategies. Governments and industry bodies are enforcing stricter environmental regulations, pushing manufacturers to adopt greener, more sustainable practices. At the same time, consumers are becoming more environmentally conscious, demanding that companies minimize their environmental impact. Digital technologies such as data analytics and AI can help manufacturers monitor their environmental footprint, optimize resource usage, and reduce waste. Furthermore, compliance with regulations can be simplified through automated systems that track and report key performance indicators (KPIs) related to environmental sustainability and safety standards.
By embracing digital transformation, manufacturers can not only enhance their competitive positioning but also meet the growing demand for sustainable practices while adhering to regulatory requirements.
Technologies Enabling Transformation
Internet of Things (IoT) and Connected Devices
The Internet of Things (IoT) plays a pivotal role in the digital transformation of manufacturing. By connecting physical devices, machines, sensors, and other equipment to the internet, IoT enables real-time data collection and analysis throughout the entire production process. Sensors embedded in machinery can monitor performance, detect anomalies, and predict when maintenance is needed, minimizing downtime. Additionally, IoT enhances visibility across the supply chain, improving decision-making and operational efficiency. With IoT-enabled devices, manufacturers can track everything from inventory levels to machine health, allowing them to respond quickly to issues and optimize operations.
Artificial Intelligence (AI) and Machine Learning (ML)
Artificial Intelligence (AI) and Machine Learning (ML) are transforming manufacturing by automating complex decision-making processes, enhancing predictive analytics, and optimizing production lines. AI-powered systems can analyze vast amounts of data, uncovering patterns and insights that would be impossible for humans to detect. Machine learning algorithms enable machines to learn from data and improve their performance over time, leading to greater process efficiencies, fewer defects, and more accurate demand forecasting. AI-driven robotics, for example, can automate repetitive tasks, while AI-powered quality control systems can identify product defects early in the production process, ensuring higher-quality outputs.
Cloud Computing and Edge Computing
Cloud computing has revolutionized manufacturing by providing scalable, flexible, and cost-effective solutions for data storage, processing, and analytics. Manufacturers can store and process vast amounts of data from production lines and machines in the cloud, enabling better insights and decision-making without the need for expensive on-premises infrastructure. Cloud solutions also promote collaboration across different departments and locations, allowing teams to access critical data in real time.
Edge computing, on the other hand, brings computation and data storage closer to the source of data generation—on the factory floor or within connected devices. This approach reduces latency and bandwidth usage by processing data locally before sending it to the cloud, making real-time decision-making possible. Combining cloud and edge computing enables manufacturers to harness the best of both worlds: centralized processing power and localized data analysis.
Robotics and Automation
Robotics and automation technologies are central to transforming manufacturing by increasing production efficiency, accuracy, and flexibility. Robotic arms, automated guided vehicles (AGVs), and autonomous mobile robots (AMRs) can handle repetitive, dangerous, or complex tasks with high precision. Automation reduces human error, enhances safety, and speeds up production cycles. Furthermore, advanced robotics can be integrated with other technologies like AI and IoT, creating intelligent systems that can adapt to changing conditions in real-time. Automation also allows for more flexible manufacturing systems, where production lines can be quickly reconfigured to produce different products without extensive downtime or manual reprogramming.
Digital Twins and Simulation
Digital twins refer to virtual replicas of physical assets, processes, or systems. These digital representations allow manufacturers to simulate, monitor, and optimize the performance of equipment, production lines, and entire factories in real-time. By using sensors and data from the physical world, digital twins provide an ongoing, up-to-date model of a product or process, which can be used to predict potential issues, assess performance, and test new scenarios before making physical changes. Simulation models help manufacturers experiment with different variables and strategies without disrupting actual operations, enabling faster innovation and more informed decision-making. Digital twins and simulation are key tools in improving product design, enhancing production processes, and increasing operational efficiency.
Together, these technologies—IoT, AI/ML, cloud and edge computing, robotics, and digital twins—are reshaping the manufacturing landscape, driving greater efficiencies, flexibility, and innovation across the industry.
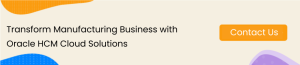
Benefits of Digital Transformation
Benefits of Digital Transformation in Manufacturing
1. Improved Operational Efficiency
- Automation of Repetitive Tasks: Digital technologies like IoT, robotics, and AI help automate tasks, reducing the need for manual labor and minimizing human error.
- Streamlined Workflows: Automation and smart technologies optimize workflows, helping to eliminate inefficiencies and bottlenecks.
- Real-time Monitoring: Manufacturers can monitor every aspect of production in real-time, allowing for quick adjustments and ensuring smooth operations.
- Increased Throughput and Productivity: By reducing lead times and optimizing resource allocation, companies can increase throughput, improve productivity, and achieve higher profitability.
2. Enhanced Product Quality and Customization
- AI-powered Quality Control: Advanced quality control systems powered by AI, digital twins, and IoT sensors allow manufacturers to detect defects in real-time, ensuring higher-quality products.
- Mass Customization: Digital technologies enable manufacturers to easily adapt production lines to meet specific customer demands, offering customized products at scale.
- Customer Satisfaction: Higher-quality products and the ability to meet individual customer preferences can lead to improved customer satisfaction and a competitive market advantage.
3. Real-time Data Analytics for Better Decision-making
- Access to Real-time Data: With IoT sensors, AI, and cloud-based analytics platforms, manufacturers gain instant access to data on production performance, supply chain operations, inventory levels, and customer demand.
- Data-driven Insights: Real-time analytics enable informed decision-making, process optimization, and proactive responses to potential disruptions.
- Predictive Analytics: By using predictive analytics, manufacturers can forecast demand, optimize supply chains, and identify opportunities for continuous improvement, ensuring they stay ahead of market trends.
4. Reduced Downtime and Maintenance Costs
- Predictive Maintenance: Using IoT sensors and machine learning, manufacturers can predict when equipment will fail and schedule maintenance before problems arise, minimizing unexpected breakdowns.
- Lower Emergency Repairs: Proactive maintenance reduces the need for costly emergency repairs and unplanned downtime, leading to more efficient production.
- Extended Equipment Lifespan: Continuous analysis of machine performance helps extend the lifespan of equipment, reducing overall maintenance costs.
5. Greater Sustainability and Reduced Waste
- Optimized Resource Usage: By integrating IoT, AI, and data analytics, manufacturers gain better visibility into resource consumption, energy usage, and waste generation.
- Energy Efficiency: AI can optimize energy consumption by ensuring machines operate efficiently, reducing excess energy use.
- Minimized Waste: Real-time data helps manufacturers optimize material usage, and digital twins and simulations allow for virtual testing of processes to minimize physical waste during experimentation.
- Sustainable Supply Chains: Data-driven insights help streamline the entire supply chain, reducing waste, improving sustainability, and aligning with environmental goals and regulatory requirements.
Steps to a Successful Digital Transformation
1. Assessing Current Technology and Capabilities
- Evaluate Existing Systems: Review current software, hardware, and data management tools to identify strengths and limitations.
- Identify Gaps: Pinpoint areas where technology is hindering efficiency, growth, or innovation.
- Set a Baseline: Establish key performance indicators (KPIs) to measure the progress of the transformation.
- Integrate Oracle HCM Cloud: Work with experts like Kovaion to evaluate how Oracle HCM Cloud can optimize HR processes, talent management, and employee engagement to support the transformation.
2. Building a Digital Strategy and Roadmap
- Align with Business Goals: Define the digital transformation goals and align them with broader business objectives such as efficiency, cost reduction, and enhanced product quality.
- Technology Selection: Identify which digital tools and platforms will be implemented (e.g., IoT, AI, cloud solutions, Oracle HCM Cloud).
- Timeline and Resources: Develop a clear timeline and allocate resources for the adoption of new technologies.
- Leverage Oracle HCM Cloud: Ensure that HR processes are aligned with digital goals by including Oracle HCM Cloud as a critical solution to optimize human capital management.
3. Investing in Training and Skill Development
- Up-skill Employees: Provide training to employees so they are equipped with the skills necessary to use new technologies like IoT, AI, and robotics.
- Promote Digital Literacy: Ensure the workforce understands how digital tools, including Oracle HCM Cloud, can enhance their roles and improve efficiency.
- Employee Engagement with Oracle HCM Cloud: Focus on training HR teams to use Oracle HCM Cloud for talent management, performance evaluations, and employee development to build a future-ready workforce.
- Continuous Learning: Foster an environment of continuous learning to keep pace with rapidly evolving technologies and industry trends.
4. Partnering with Technology Providers and Consultants
- Select the Right Partners: Identify reliable technology providers who can offer cutting-edge solutions to drive digital transformation, including IoT, AI, and cloud computing.
- Strategic Consultation: Engage consultants who can guide the strategic aspects of transformation, ensuring technology aligns with business needs.
- Oracle HCM Cloud Expertise: Partner with experienced consultants like Kovaion for the implementation of Oracle HCM Cloud, ensuring smooth integration and optimization of HR systems to enhance talent management and employee engagement.
- Seamless Integration: Ensure that new technologies, including Oracle HCM Cloud, integrate smoothly with existing systems to avoid disruptions and improve overall efficiency.
Future Trends in Manufacturing
1. Expansion of Autonomous Manufacturing
- Increased Automation: The rise of autonomous manufacturing will lead to more self-operating systems in production lines, reducing human intervention and increasing efficiency.
- AI and Robotics: Autonomous systems, powered by AI and robotics, will perform tasks like assembly, inspection, and packaging without human input, improving consistency and speed.
- Adaptive Production: These systems will be able to adapt to changes in demand or production requirements in real-time, allowing for flexible and scalable operations.
- Reduced Labor Costs: Autonomous manufacturing can help companies reduce labor costs while improving productivity and safety on the shop floor.
- Integration with IoT: Autonomous machines will communicate with IoT devices for real-time monitoring and control, enabling continuous optimization of the production process.
2. Role of 5G in Manufacturing Connectivity
- Faster Data Transfer: 5G will enable faster, more reliable communication between devices, systems, and machines across the manufacturing floor, leading to improved operational efficiency.
- Real-time Data Sharing: With 5G, manufacturers will be able to transmit large volumes of data instantaneously, facilitating real-time decision-making and process adjustments.
- Remote Control and Monitoring: 5G networks will enable remote monitoring and control of machines, reducing the need for on-site personnel and enhancing operational flexibility.
- Enhanced IoT Connectivity: 5G will boost the performance of IoT devices by providing low latency and high-speed connections, ensuring seamless communication between connected devices in a smart factory.
- Enabling Industry 4.0: The deployment of 5G will accelerate the adoption of Industry 4.0 technologies, including IoT, AI, and machine learning, within manufacturing environments.
3. Increased Use of Predictive and Prescriptive Analytics
- Predictive Maintenance: Predictive analytics will continue to grow, allowing manufacturers to foresee when equipment is likely to fail and schedule maintenance accordingly, preventing unplanned downtime.
- Improved Decision-Making: Prescriptive analytics will help manufacturers identify optimal actions and strategies to improve production efficiency, reduce waste, and cut costs.
- Demand Forecasting: Manufacturers will use advanced analytics to predict consumer demand more accurately, allowing for better inventory management and reducing the risk of overproduction or stockouts.
- Process Optimization: Data-driven insights will help optimize manufacturing processes, enabling continuous improvements in quality, speed, and efficiency.
- Supply Chain Optimization: Predictive and prescriptive analytics will enhance supply chain visibility and decision-making, improving procurement strategies and logistics operations.
4. Growing Focus on Cybersecurity and Resilience
- Rising Cyber Threats: As manufacturing becomes more digitally connected, the risk of cyberattacks targeting critical infrastructure will increase, making cybersecurity a top priority.
- Protecting Data and Systems: Manufacturers will invest in advanced cybersecurity solutions to protect their digital assets, including intellectual property, sensitive production data, and customer information.
- Resilience Planning: Manufacturers will develop resilience strategies to ensure the continuity of operations in the event of cyberattacks, natural disasters, or other disruptions.
- Adoption of Secure IoT: With the expansion of IoT in manufacturing, ensuring that all connected devices are secure will be essential to protect the network and data.
- Regulatory Compliance: As cybersecurity regulations evolve, manufacturers will need to comply with industry standards and government mandates to avoid penalties and protect their operations.
Technologies Enabling Transformation
Oracle HCM Cloud: Empowering Workforce Transformation in Manufacturing
- Enhancing Workforce Management: Oracle HCM Cloud provides a comprehensive suite of tools to streamline workforce management, enabling manufacturers to optimize their human resource processes from recruitment to retirement. This includes automated workflows for hiring, performance management, training, and career development, helping manufacturers align their talent strategy with business goals.
- Improving Employee Engagement: Employee engagement is crucial to the success of digital transformation in manufacturing. Oracle HCM Cloud offers tools for real-time communication, feedback, and recognition, which helps improve morale and retention. With features such as employee surveys, performance reviews, and goal setting, it fosters a more engaged and motivated workforce.
- Skills and Training Development: As manufacturing evolves with new technologies, it is essential for employees to have the right skills. Oracle HCM Cloud supports learning management systems (LMS) that allow manufacturers to develop customized training programs. These programs help workers adapt to new digital tools, such as IoT devices or robotics, improving the overall productivity of the workforce and accelerating digital transformation.
- Real-Time Workforce Analytics: With Oracle HCM Cloud, manufacturers gain access to real-time workforce analytics that provide insights into employee performance, productivity, and skills gaps. These insights help manufacturing leaders make data-driven decisions, such as reallocating resources or providing targeted training, thereby enhancing operational efficiency.
- Seamless Integration with Other Digital Tools: Oracle HCM Cloud integrates seamlessly with other digital transformation technologies, such as AI, IoT, and cloud computing, enhancing the overall efficiency and effectiveness of manufacturing operations. This integration enables a unified approach to employee management and manufacturing processes, where workforce data can be used to optimize production performance.
- Support for Digital Workforce Transformation: The digital transformation in manufacturing is not just about machines and technologies, but also about the workforce that supports them. Oracle HCM Cloud helps manufacturers manage the evolving demands of a digital workforce, ensuring that employees have the skills, tools, and support they need to thrive in a smart manufacturing environment.
- Agility in Responding to Changing Workforce Needs: As manufacturing moves towards more agile, real-time production systems, the workforce needs to be flexible and responsive. Oracle HCM Cloud’s self-service capabilities and advanced analytics enable manufacturers to quickly adapt to changes in staffing requirements, ensuring that the right talent is available at the right time to meet production demands.
Benefits of Digital Transformation
Unlocking Workforce Potential with Oracle HCM Cloud
- Optimizing Talent Management: Oracle HCM Cloud offers a robust platform for managing the entire employee lifecycle, from recruitment to retirement. By using advanced AI and analytics, manufacturers can streamline hiring processes, ensuring they attract the best talent suited to their evolving business needs. This helps create a workforce with the right mix of skills to support digital transformation initiatives.
- Improving Workforce Efficiency: With Oracle HCM Cloud, manufacturers can automate key HR processes such as payroll, benefits administration, and performance management, freeing up HR teams to focus on strategic tasks. The platform’s self-service capabilities empower employees to manage their own HR-related tasks, improving overall workforce efficiency and reducing administrative burden.
- Employee Engagement and Retention: Oracle HCM Cloud enhances employee engagement by offering tools that facilitate real-time feedback, continuous performance tracking, and employee recognition. With features like pulse surveys and career development plans, manufacturers can ensure that employees remain motivated and satisfied, reducing turnover rates and retaining top talent.
- Driving Innovation through Workforce Skills: The platform’s integrated learning and development tools help manufacturing companies upskill their workforce to meet the demands of new technologies and production methods. By offering targeted training and personalized learning paths, Oracle HCM Cloud helps foster a culture of innovation where employees are encouraged to embrace new technologies and drive continuous improvement.
- Real-Time Workforce Analytics: Oracle HCM Cloud provides manufacturers with real-time insights into workforce performance and productivity. These data-driven insights allow HR leaders to make informed decisions about staffing, skill development, and resource allocation, ensuring that the workforce is optimized for maximum output. Real-time analytics also allow manufacturers to identify skill gaps and quickly address them, driving operational excellence.
- Supporting Agility and Flexibility: As manufacturing shifts towards more agile and dynamic production methods, Oracle HCM Cloud provides the flexibility needed to manage a changing workforce. Whether responding to fluctuating production demands or adjusting team structures for new projects, the platform’s flexible features enable manufacturers to easily adapt to the evolving needs of the business.
- Streamlining Collaboration and Communication: Oracle HCM Cloud includes collaboration tools that connect employees across different departments and locations. By facilitating better communication and information sharing, the platform ensures that teams work more effectively together. This collaboration boosts overall productivity and accelerates innovation in the manufacturing process.
- Aligning Workforce Goals with Business Objectives: Oracle HCM Cloud helps align individual and team goals with the broader objectives of the manufacturing business. With its performance management and goal-setting tools, manufacturers can ensure that every employee is focused on achieving outcomes that contribute to the company’s strategic initiatives, from operational improvements to digital transformation goals.
- Improving Compliance and Risk Management: The platform offers comprehensive tools for managing compliance and regulatory requirements, ensuring that manufacturers meet industry standards and avoid penalties. By automating compliance tracking and reporting, Oracle HCM Cloud reduces the risk of human error and helps manufacturers stay compliant with labor laws and other regulatory guidelines.
Transform Your Manufacturing Business with Oracle HCM Cloud Solution
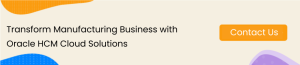
Ready to take your manufacturing operations to the next level? Explore how Oracle HCM Cloud can accelerate your digital transformation journey. With Kovaion as your trusted Oracle partner, we offer end-to-end Oracle HCM Cloud solutions tailored to enhance your workforce management, boost efficiency, and drive growth. Contact us today to learn how we can help you transform your business!